Thursday, May 5, 2011
The Inside Takes Shape
Tuesday, April 26, 2011
The Barn House


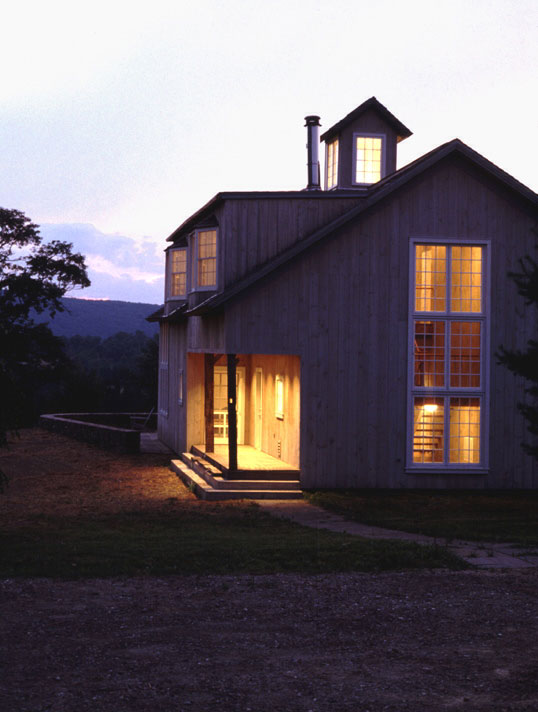

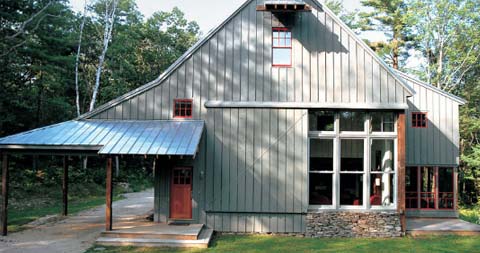
Thursday, April 7, 2011
Saturday, January 29, 2011
Enclosure
Since timber frames are load bearing structures in themselves, there are many options for insulation beyond 2x walls with fiberglass or foam between the studs. Ideally you utilize a system that doesn’t involve the redundancy of another load bearing wall attached to the timber frame. We often install panels on timber frames we build, but wanted to explore other methods in our own house. Our plan was to build double stud walls and then blow in cellulose for insulation. This would allow us to use a recycled product to create a wall with a high r-value. Building our own insulation system would also mean using our labor, rather than paying the panel company to pre-build and cut the panels. In the end however, it seemed like we might never have walls if we didn’t go the panel route—so that is what we did and thirteen days after the panels arrived we had a weather tight structure. It is still a thrill for me to pull in the driveway and see a building with windows, but I imagine it is only a matter of time before the beauty of black felt paper and orange cap nails wears thin and I yearn for siding and a porch.
Monday, December 13, 2010
Lights

In a timber frame that is insulated with panels, the lighting has to be planned earlier in the process than in a conventionally framed house. There are minimal places in which to hide wires and no wall or roof cavities. As a result, on a very cold recent evening we found ourselves laying out future hanging lights on the sawdust covered floor and using a laser to project the location onto the ceiling. Holes were

In my efforts to rapidly educate myself about lighting placement and options, I have learned that there are basically three types of lighting that one should think about- general, task and accent. Also, in a house with an open floor plan, such as this one, it is possible to differentiate the spaces through creating unique lighting scenarios is each.

Since we used rough sawn lumber that is somewhat weathered in places, I am going to go with a theme of utilitarian light fixtures throughout the house. These barn inspired fixtures seem to be quite popular right now and are prevalent on Amazon and at Ikea. I am hoping they will contrast well with the wood frame and floors and the plaster covered walls. And while lighting placement will be tricky to change, the fixtures themselves can be swapped out easily to create an entirely different look.
Wednesday, November 24, 2010
Finally...
Each warm and sunny summer month came and went without making any progress on our house. We did, however, raise two other peoples’ house frames and a large barn. We also built custom cabinets for a big kitchen, as well as completed a number of smaller projects. The tarp covering our foundation became tattered and I really wondered if we would put our own timber frame up before there was snow on the ground. Then last Thursday, a week before Thanksgiving, the crane was on site and we managed to raise the whole frame in a day.
And now the panels and windows are ordered and when they are installed we will have an enclosed, weather tight structure. We are using structural panels on the walls and nail base panels over tongue and groove decking on the roof. The panels will arrive precut for our house frame with window and door openings already in place.
This slightly euphoric state, right after the timber frame goes up, is one that we are well acquainted with in homeowners. After months of seeing the plan on paper only, it is finally a three dimensional reality. While it is a great joy to pull into the driveway and see our future house rising above the foundation, I am incredibly daunted by the many layers that lie ahead. Sure, if we had lots of money to throw at the project it would get done in a timely manner, but this is after all an experiment in doing more with less and we will see it through to the end, even if it means a few months living in the basement.
Friday, April 16, 2010
The Mod



